How a Paint Pigging System Optimizes Efficiency and Reduces Waste in Paint Manufacturing
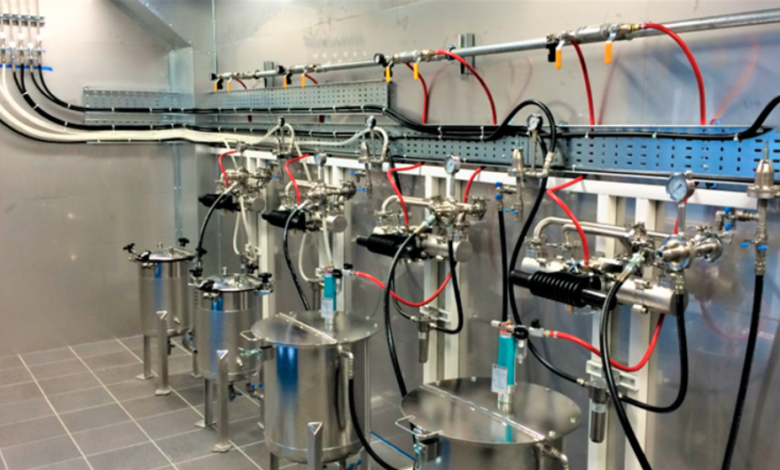
In the competitive world of industrial and decorative coatings, paint manufacturers constantly face the challenge of reducing waste, minimizing color contamination, and maximizing yield. One proven, cost-effective technology that addresses all three is the paint pigging system. This method, which involves using a pig (a solid device) to recover residual product from inside pipelines, is rapidly gaining ground in the paint industry due to its operational, financial, and environmental benefits.
In this article, we’ll explore how a paint pigging system works, why it’s ideal for modern paint production environments, and how companies can benefit from implementing it across their production lines.
Understanding the Basics: What Is a Paint Pigging System?
A paint pigging system is a process used in liquid handling operations, where a projectile—called a pig—is sent through a pipe to push out leftover product, clean the line, or separate batches. In the case of paints, where viscosity is high and contamination can easily occur, pigging becomes crucial.
The pig is typically made of a flexible, food-grade or solvent-resistant material that tightly conforms to the pipeline’s diameter. It is propelled by compressed air, nitrogen, or another fluid. This process ensures that nearly all remaining paint in a line is recovered for use rather than washed away during cleaning.
See also: self loading mixer: The Evolution of Concrete Mixing Technology on Construction Sites
Why the Paint Industry Needs Pigging More Than Ever
Paint production lines frequently deal with a wide range of colors and formulations. Each product switch can mean extensive cleaning, resulting in product loss and longer downtime. A paint pigging system minimizes this by:
- Recovering high-value paints from the pipeline
- Reducing the volume of solvents or water needed for cleaning
- Preventing cross-contamination between colors or batches
- Accelerating changeover times
- Lowering hazardous waste generation
Whether you’re manufacturing architectural coatings, industrial paints, or automotive lacquers, pigging offers consistent, scalable advantages.
Key Components of a Paint Pigging System
For a pigging system to function efficiently in paint applications, several elements must work in harmony:
1. Pig
The heart of the system, the pig is a cylindrical object made from durable, chemical-resistant materials like silicone, polyurethane, or elastomers. It forms a seal inside the pipe and pushes the paint forward while wiping residual paint off the inner wall.
2. Pig Launcher and Receiver
These components are placed at either end of the pipeline. The launcher inserts the pig, while the receiver safely collects it after its journey through the pipe.
3. Detection Sensors
Sensors placed at various points in the system track the pig’s location to ensure safe and accurate operation.
4. Control Unit
Most modern paint pigging systems are integrated with a PLC or SCADA system that automates pig movement, cleaning sequences, and safety interlocks.
5. Propulsion Medium
Air, nitrogen, or a compatible liquid is used to move the pig through the pipe at a controlled speed.
Each component must be tailored to the paint being handled, pipeline geometry, and the degree of automation required by the facility.
Applications of Paint Pigging Systems
Pigging is widely used in different types of paint production, including:
- Decorative Paints: Fast color changeovers and prevention of shade mixing.
- Automotive Coatings: High-precision, clean line transitions.
- Protective and Industrial Coatings: Recovery of viscous, high-value paints that would otherwise be lost.
- Water-Based and Solvent-Based Paints: Systems are designed to handle both types, with special care taken for explosion-proof requirements in solvent-based lines.
Advantages of Implementing a Paint Pigging System
The benefits of a paint pigging system span several dimensions—operational, environmental, and financial.
1. High Product Recovery
Pigging typically recovers up to 99.5% of the paint remaining in the pipeline after a batch. This drastically reduces product waste and increases overall yield.
2. Reduced Use of Cleaning Chemicals
Since the pig pushes most of the paint out of the line, less solvent or water is needed for flushing. This reduces chemical costs, minimizes emissions, and shortens cleaning cycles.
3. Faster Color Changeovers
Paint lines often switch between many colors per day. Pigging speeds up this process, reducing line downtime and improving flexibility in production scheduling.
4. Environmental Compliance
Less paint waste and reduced solvent use mean fewer emissions and better compliance with environmental regulations such as EPA or REACH standards.
5. Better Quality Control
The chance of cross-contamination is significantly reduced when residual paint is effectively removed from the line, ensuring batch integrity and consistent quality.
6. Return on Investment (ROI)
Although the initial cost of a paint pigging system can be significant, many companies see payback within a year through savings on product, solvents, water, and labor.
Key Factors for Successful Implementation
When installing a paint pigging system, several key factors must be considered:
- Pipeline Material and Layout: Smooth, stainless-steel pipes with minimal bends or obstructions yield better pigging performance.
- Paint Characteristics: Viscosity, curing time, and pigment type all influence the type of pig and system required.
- Automation Level: Automated systems allow for hands-free operation, but semi-manual systems can also be effective for smaller operations.
- Safety: Solvent-based paints may require ATEX-certified or intrinsically safe systems to prevent ignition in flammable environments.
The Future of Paint Production: Cleaner, Faster, and More Sustainable
As manufacturers continue to face rising raw material costs, tighter environmental regulations, and the demand for high-quality, custom-colored products, pigging will become an even more integral part of paint production.
Modern paint pigging systems are being developed with smarter automation, self-cleaning capabilities, and even real-time data logging. Integration with Industry 4.0 platforms allows predictive maintenance and deeper process insights.
Conclusion
The paint pigging system is a game-changing solution for modern paint manufacturers looking to enhance efficiency, reduce waste, and stay competitive. It’s not just a cleaning tool—it’s a complete productivity solution that ensures every drop of paint counts.
Whether your facility is small-scale or a high-output operation, pigging can be tailored to your needs and scaled across multiple lines. From product recovery to environmental compliance, the benefits are broad, tangible, and sustainable.